Thermo King Motor Drive for Bus HVAC Applications
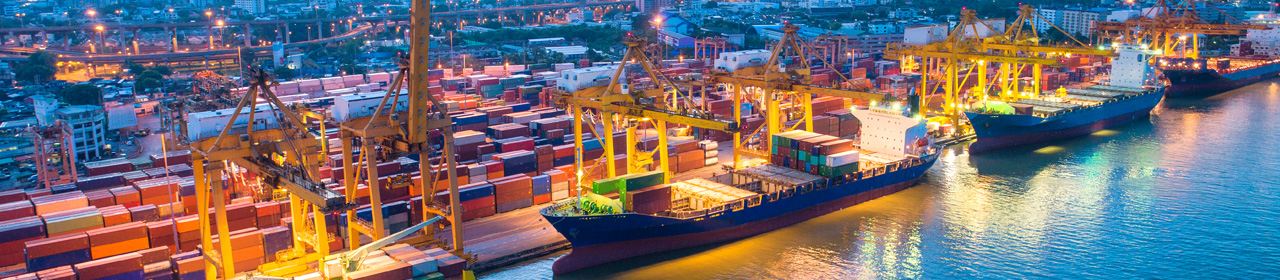
The purpose of the Thermo King Motor Drive is to convert the 27V DC power from the bus to AC 20V 3 phase power to the HVAC system to operate the inverter duty brushless evaporator and condenser motors. The inverter provides the conversion from an irregular DC current to a stable AC current environment.
To be an effective inverter, the Thermo King motor drive was designed to work with the evaporator and condenser motors as a matched set. Meaning the input and output of each has a direct relationship to the functionality of the unit. The inverter is required to produce a motor speed range of 825 (evaporator low speed) to 1910 RPM (condenser high speed) to maintain proper airflow. Lack of proper airflow can create multiple ill effects throughout the system and damage to the motors. If the inverter is not commanding the proper motor speed output the unit airflow is reduced such that there is insufficient warm air flowing through the evaporator coil and incomplete evaporation of the refrigerant. The thermal expansion bulb senses the lack of super heat in the refrigerant and begins to close, reducing the evaporation temperature of the refrigerant (high discharge pressure). As this condition continues, freezing of the condensate on the bottom of the coil could begin (low suction pressure). Also, the closing of the expansion valve reduces the refrigerant flow back to the compressor causing poor oil return and reduced cooling of the compressor, and could result in eventual compressor failure.
Thermo King New Motor Drives
Thermo King provides new motor drives.They are either sold as new, or sold under a reman number to accommodate customers that prefer to exchange cores. The motor drive sold as reman are new, they are not rebuilt and not remanufactured. The motor drives are built in a controlled environment, each are tested and meet the original design and output specifications.
Competitive Repair Shops
There are competitors that market their products as remanufactured but they are merely repaired. The motor drive is a proprietary assembly (Table I.). As a result, competitors that repair the motor drives do not have access to update boards to the most current revisions. They cannot replicate the main microchip therefore cannot replace it and they do not have access to the output specifications and are tested to very limited standards. In most cases, the repairs they make are cosmetic.
An analysis of a competitor rebuild motor drive was conducted and compared to the design specifications. The results showed the cosmetic repairs, no attempt to repair either of the two boards within the assembly. The results of a power up test showed the motor drive power supply measured at 27.79 DCV, within the range of acceptable DC. The unit failed the motor test achieving a maximum speed of 78 RPM when required to produce a motor speed range of 825 to 1910 RPM. Lack of proper repair and test specifications can ultimately produce inconsistent and unreliable results.
The transit authority must determine the tradeoff between a higher upfront cost of the Thermo King motor drive and a lowered cost repaired motor drive. On the one hand, operating an air-conditioning system with a motor drive that can achieve consistent motor speed that will provide the air out put needed to reach the desired interior air temperature and reduce potential damage to motors and other components in the system. Or operating the system with a motor drive that has been repaired that may have unpredictable airflow out-put and over all life of the component and the potential of unforeseen more expensive failures and unscheduled loss of service.
he controller firmware is updated to the latest factory release including engineering changes that impact safety, reliability and performance. In an environment that is controlled to protect the product. Humidity levels are closely monitored and electrostatic discharge and product handling controls are in place to protect the sensitive components on the control circuit boards. Factory production test equipment will test the control components across its range of function and to current manufacturing standards, not just at a few test points.