Impressively Lean
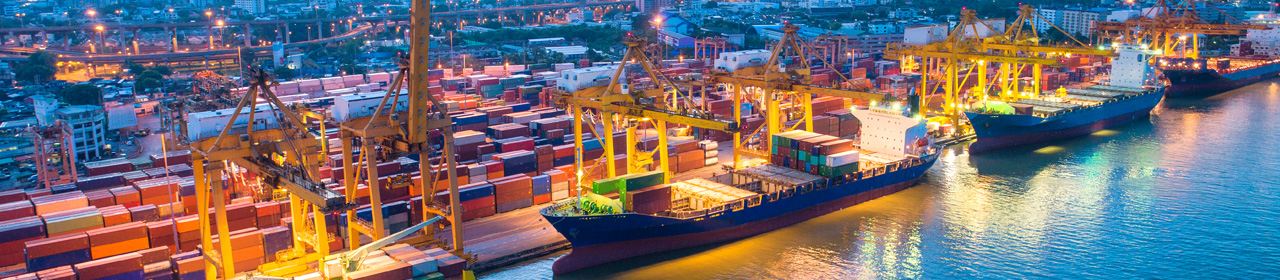
Since 2010, Thermo King’s Wujiang plant in China has been specializing in the company’s marine product range. Impressive from the beginning, the 72,000 m2 facility with an internal covered space equal to the size of nine football fields, Wujiang is truly a one-stop-shop when it comes to manufacturing the MAGNUM®, SG genset and SuperFreezer lines.
“We enjoy bringing customers to Wujiang because in one visit, they can view the production of all our marine products,” said Michel van Roozendaal, vice president and general manager, Thermo King Marine Solutions. “The operation is even more impressive following a three-year lean transformation that resulted in streamlined processes and production efficiencies that are translating to faster outturn of product.”
With strong company-wide support, the plant was able to further improve processes and implement lean strategies that made a fast impact on output and quality. From order entry through the shipping of finished product, Wujiang decreased its cycle time by 50 percent in 2013, allowing a faster response to customer demand.
A flexible production system was implemented to reduce ramp up time so that customer needs can be met when demand is high, yet at the same time accommodate the normal fluctuation of the industry. At the foundation of this system is a standard work station ‘operation playbook’ that outlines the total solution and requirements needed to meet various production outputs. In addition, a new computerized system was put in place to support and monitor the production line in real time. Status is shown on a monitor allowing management and a support function team to check status in real time, from their office, and an alarm is automatically launched if issues need to be addressed.
These planning and organizational efforts allow Wujiang to meet unanticipated demands and overcome unexpected challenges.
“In the second half of last year, there was a big increase in customer orders, which is always a good thing. The processes we had in place allowed us to react quickly and avoid a backlog,” said Mark Tu, Wujiang focus factory manager. “Within 60 days, we promptly hired 121 shop floor employees, gained the needed material supply, and ramped up from 20 units per day to 70 units per day achieving 100 percent on-time delivery.”